The market for Professional Powder Coating Kit options is driven by industrial facilities, commercial shops, and large-scale manufacturers requiring high-volume, high-quality coating solutions. These kits meet demand for durable finishes on metal components used in automotive, aerospace, construction, and machinery industries. Prices for Professional Powder Coating Kit range from $5,000 for mid-tier systems to over $20,000 for industrial-grade setups, with costs tied to oven capacity, gun performance, and automation features.
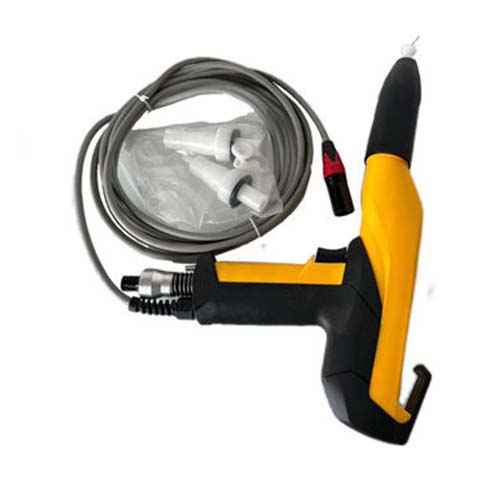
Professional Powder Coating Kit is designed for large-scale, high-precision projects such as coating automotive frames, industrial machinery parts, metal roofing panels, and aerospace components. These projects often involve high-volume production or large items requiring uniform, long-lasting finishes that withstand extreme conditions (heat, chemicals, heavy use). Whether a facility is coating 100+ parts daily or handling oversized metal sheets,
Professional Powder Coating Kit provides the power and consistency to meet industrial standards.
Professional Powder Coating Kit relies on advanced surface treatment technologies to ensure optimal adhesion and finish quality. The process begins with automated cleaning systems—alkaline cleaners or ultrasonic baths remove heavy grease, oil, and contaminants from large batches of parts. Next, industrial-grade sandblasting or shot peening equipment (integrated with many
Professional Powder Coating Kit setups) creates a uniform surface profile, eliminating rust, scale, and old coatings. Post-treatment includes phosphate conversion coating or chromate passivation, enhancing corrosion resistance. These steps, critical for professional results, ensure powder from the Professional Powder Coating Kit bonds tightly to even the most demanding metal surfaces.
A
Professional Powder Coating Kit is a heavy-duty, industrial-caliber system engineered for commercial and manufacturing environments. Unlike consumer kits, it features high-capacity components, advanced controls, and automation options to handle continuous operation. It enables electrostatic application of specialized powders (resistant to extreme temperatures, chemicals, and abrasion) followed by curing in large, precision ovens. Professional Powder Coating Kit is built for reliability, consistency, and scalability, making it essential for businesses requiring repeatable, high-performance finishes on metal parts.
Industrial Powder Coating Gun System: A key component of any Professional Powder Coating Kit, it includes high-voltage (50-100kV) guns with adjustable output, designed for high-volume application. Many feature automated nozzles or robotic arms for consistent coverage on complex parts, reducing waste and ensuring uniformity across batches.
Large-Scale Curing Oven: Professional Powder Coating Kit ovens range from 10 to 50+ cubic feet, accommodating large parts (e.g., automotive chassis) or multiple batches. They offer precise temperature control (300-500°F) with digital thermostats, forced-air circulation, and zone heating to ensure even curing, critical for thick or multi-layer coatings.
Powder Management System: Included in Professional Powder Coating Kit setups, this features large hoppers (50+ pounds), automated powder feeding, and recovery systems to recycle overspray. It ensures a steady supply of powder to guns, reduces waste, and supports quick color changes for versatile production needs.
Professional Powder Coating Kit options deliver distinct benefits for industrial users. First, they boost productivity: high-capacity ovens and automated guns handle 10x more parts than consumer kits, reducing per-unit coating time. Second, they ensure consistency: advanced controls (digital temperature monitoring, pressure regulators) produce uniform finishes across thousands of parts, meeting strict quality standards. Third, they support versatility: compatible with specialized powders (high-heat, anti-corrosive, textured) for diverse industries, from automotive to marine. Finally, they lower long-term costs: powder recovery systems reduce waste by 80%+, and durable finishes minimize rework, making Professional Powder Coating Kit a smart investment for scaling operations.
Choosing the right
Professional Powder Coating Kit starts with assessing production volume. For small commercial shops (50-100 parts/day), a mid-tier kit with a 15-20 cubic foot oven and semi-automated guns suffices. For large factories (1000+ parts/day), opt for industrial-grade systems with 30+ cubic foot ovens, robotic application arms, and integrated powder recovery. Check oven temperature uniformity—look for ±5°F variance to avoid finish inconsistencies. Evaluate gun compatibility with specialty powders (e.g., metallic, high-temperature) if your projects require them. Consider energy efficiency: models with insulated ovens and variable speed fans reduce utility costs. Reading case studies of similar facilities using the Professional Powder Coating Kit can also guide decisions, ensuring the system matches your workflow.
Operating a
Professional Powder Coating Kit for high-volume production requires systematic setup. Start by calibrating the gun: adjust voltage (50-80kV for most metals) and powder flow rate (based on part size) using the kit’s digital controls. Preheat the oven to the powder’s specified temperature (375-450°F) and verify uniformity with a thermal sensor. Load parts onto an automated conveyor (included in many Professional Powder Coating Kit setups) to ensure consistent spacing, preventing overlap during coating. Apply powder in two passes: a light first coat to cover surface imperfections, then a second coat for desired thickness (2-5 mils). Cure parts for the recommended time (15-30 minutes) before cooling on a separate conveyor. Regularly check powder levels in the hopper and clean gun nozzles every 2 hours to maintain flow—steps that keep the Professional Powder Coating Kit running efficiently during long production runs.
Maintaining a Professional Powder Coating Kit prevents downtime and ensures consistent performance. Daily tasks include cleaning gun nozzles with compressed air, emptying excess powder from the recovery system, and wiping down conveyor belts to remove residue. Weekly, inspect oven heating elements for corrosion and replace worn gaskets to maintain temperature control. Monthly, deep-clean the powder hopper and feed lines to prevent clogs, and lubricate moving parts (conveyor chains, gun hinges) to reduce friction. Quarterly, calibrate the oven’s thermostat and gun’s voltage settings using professional tools—this ensures the Professional Powder Coating Kit meets performance specs. Keep a log of maintenance checks and replace parts (e.g., filters, hoses) per the manufacturer’s schedule, as worn components can compromise finish quality.
Troubleshooting finish defects with a
Professional Powder Coating Kit starts with identifying the issue. If finishes have pinholes, check for surface contamination—increase cleaning time in the pre-treatment stage. For orange peel texture, reduce powder flow rate or adjust the gun’s distance from parts (8-12 inches is optimal). If edges are too thick (runs), lower the gun’s voltage when coating sharp edges. For uneven curing, verify oven temperature with an external probe—replace a faulty heating element if discrepancies exist. If powder adheres poorly, check part grounding (ensure conveyor rails are clean and conductive). Most defects with a Professional Powder Coating Kit stem from inconsistent setup or worn components, so regular calibration and maintenance often resolve issues before they affect production.
Safety with a
Professional Powder Coating Kit is critical in industrial settings. Equip operators with respiratory protection (N95 masks or powered air-purifying respirators) to filter powder particles. Install ventilation systems (local exhaust hoods near the gun) to reduce airborne powder. Train staff to use heat-resistant gloves when loading/unloading the oven, which reaches extreme temperatures. Ensure the workspace is grounded—connect all equipment to a common ground to prevent static sparks. Store powder in sealed, fire-resistant cabinets away from ignition sources. Post clear safety protocols (e.g., no open flames, emergency shutdown procedures) near the Professional Powder Coating Kit. Regularly inspect electrical components (cables, plugs) for damage and keep a Class D fire extinguisher nearby, as powder is combustible in high concentrations. These measures protect workers and prevent accidents with the Professional Powder Coating Kit.
Disclaimer: Enhance your coating process with advanced electrostatic powder coating machines, precision powder coating spray guns, comprehensive powder coating systems, and efficient powder coating lines from Hangzhou Huaxiang Coating Equipment Co., Ltd. Designed for reliability and high-quality finishes, our solutions meet all your industrial powder coating machine needs. Contact us at sale3@cncolourspray.com