In the dynamic landscape of modern manufacturing, Electrostatic Powder Coating Machines have emerged as indispensable tools, renowned for their ability to deliver top - notch coating results. Let's embark on an in - depth exploration of these remarkable machines.
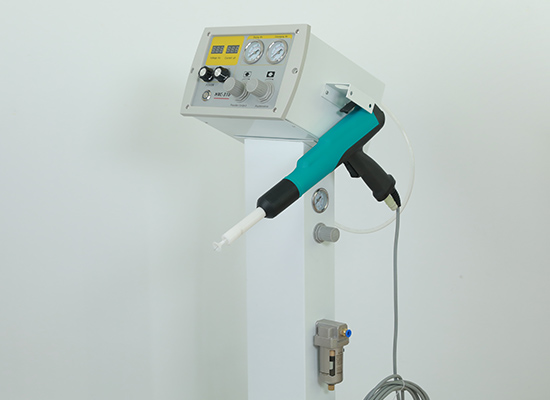
1. Introduction and Structure of Electrostatic Powder Coating Machine
An
Electrostatic Powder Coating Machine is a sophisticated system composed of several key components. The powder supply system serves as the reservoir, carefully storing and precisely delivering the powder material. It ensures a consistent flow of powder, which is crucial for uniform coating. The electrostatic spray gun is the star of the show. It imparts an electrostatic charge to the powder particles, enabling them to be attracted and adhere firmly to the grounded workpiece. A reliable grounding device is essential to complete the electrostatic circuit, guaranteeing the effectiveness of the powder - to - workpiece adhesion. Finally, the curing oven plays a vital role in the process. It subjects the coated workpiece to the right temperature and time, solidifying the powder coating into a tough, durable finish.
2. Application Scenarios
The versatility of
Electrostatic Powder Coating Machines has led to their widespread adoption across multiple industries. In the automotive sector, they are the go - to choice for coating various parts. From engine components that need to withstand high temperatures and mechanical stress to exterior body panels that demand an aesthetically pleasing and corrosion - resistant finish, these machines deliver. In the construction industry, aluminum profiles and steel structures benefit from the long - lasting protection and enhanced appearance provided by electrostatic powder coating. It helps these building materials endure harsh environmental conditions. The furniture industry also reaps the rewards, using these machines to coat metal furniture, adding both durability and a touch of elegance.
3. Equipment Price
The cost of
Electrostatic Powder Coating Machines can vary significantly based on several factors. For hobbyists or those running small workshops, entry - level small - scale machines are available at a relatively affordable price, starting from around (1000. These models are suitable for low - volume production and basic coating needs. On the other hand, large - scale industrial models equipped with advanced features such as automated powder feeding, precise multi - zone temperature control in the curing oven, and high - performance electrostatic systems can cost upwards of )50000. These high - end machines are designed to meet the demands of large - scale manufacturing operations with high production volumes and strict quality requirements.
4. Correct Usage
To achieve optimal results, following the correct usage procedure is crucial. Begin by thoroughly cleaning and degreasing the workpiece. This step is fundamental as any dirt, oil, or contaminants on the surface can prevent proper powder adhesion. Once the workpiece is clean, proceed to set the appropriate powder flow rate and voltage on the machine. These settings depend on factors such as the type of powder being used, the size and shape of the workpiece, and the desired coating thickness. When spraying, hold the electrostatic spray gun approximately 15 - 20 cm away from the workpiece and move it in a smooth, consistent motion. This ensures an even distribution of the powder. After spraying, transfer the coated workpiece to the curing oven and set the temperature and time according to the powder manufacturer's recommendations.
5. How to Choose
Selecting the right
Electrostatic Powder Coating Machine requires careful consideration. First and foremost, assess your production volume. If you have high - volume production needs, you'll need a machine with a large - capacity powder supply system and efficient curing capabilities. The type of powder you'll be using is also important. Different powders may require specific electrostatic properties and flow characteristics, so choose a machine that can accommodate them. Consider the size and shape of your workpieces as well. Larger or irregularly shaped workpieces may need a machine with a more flexible spray gun and a larger curing oven. Look for machines that offer stable electrostatic performance, as this directly impacts the quality of the coating. An easy - to - operate control panel is also a plus, as it reduces the learning curve and allows for quick adjustments. Additionally, opt for reliable brands with a proven track record and excellent after - sales service. This ensures that you can get technical support, spare parts, and maintenance assistance when needed.
6. Safety Precautions
Safety should always be a top priority when operating an
Electrostatic Powder Coating Machine. Wear appropriate protective clothing, including coveralls or aprons, to prevent powder from getting on your skin. A mask is essential to avoid inhaling powder particles, which can be harmful to your respiratory system. Gloves protect your hands from potential contact with chemicals in the powder or any electrical components. Ensure that the working area is well - ventilated. Good ventilation helps to prevent the accumulation of powder in the air, reducing the risk of dust explosions and maintaining a healthy working environment.
7. Rationality Analysis
Electrostatic Powder Coating Machines offer several advantages that make them a rational choice for many manufacturers. They are highly energy - efficient. During the curing process, they consume less energy compared to some traditional coating methods. Additionally, they use powder more efficiently, with less waste as oversprayed powder can often be recycled. The high - quality, long - lasting finish they provide means that products need less frequent re - coating, which saves both time and money in the long run. This not only benefits the manufacturer but also the end - users who get more durable products.
8. Q&A
A1: Absolutely not. The grounding device is the linchpin of the electrostatic system. It creates the necessary electrical potential difference that allows the charged powder particles to be attracted to the workpiece. Without it, the powder simply won't adhere properly, and the coating process will be ineffective.
Q2: What if the powder coating has a lot of orange peel effect?
A2: First, start by adjusting the spray gun parameters. Increase or decrease the voltage to see if it affects the powder distribution. Also, check and optimize the powder flow rate. Sometimes, an inconsistent powder flow can lead to an uneven coating. Additionally, inspect the powder quality. Low - quality powder or powder that has been contaminated may cause the orange peel effect.
Q3: How often should the powder supply system be maintained?
A3: For optimal performance, it's recommended to maintain the powder supply system every 2 - 3 months. This includes cleaning the powder hopper, checking the powder feed lines for any blockages, and ensuring that the powder - metering components are in good working order. Regular maintenance helps to ensure a consistent powder flow and high - quality coating results.
Q4: Can it coat non - metal materials?
A4: Generally, non - metal materials cannot be directly coated with an electrostatic powder coating machine. Since they are non - conductive, the powder particles won't be attracted to them in the same way as they are to metal. However, non - metal materials can be pre - treated to make them conductive. This can involve applying a conductive primer or using other surface - modification techniques, after which they can be coated using an electrostatic powder coating machine.
Q5: What are the advantages of electrostatic powder coating over liquid coating?
A5: Electrostatic powder coating has several distinct advantages. Firstly, it produces significantly less waste. Oversprayed powder can often be collected and reused, while liquid coatings typically have a higher amount of waste due to factors like solvent evaporation. Secondly, it has no volatile organic compounds (VOCs). This makes it more environmentally friendly and also reduces the need for costly ventilation and air - purification systems in the workplace. Finally, it provides a more durable finish, with better resistance to chipping, scratching, and corrosion compared to many liquid coatings.
Disclaimer: Enhance your coating process with advanced electrostatic powder coating machines, precision powder coating spray guns, comprehensive powder coating systems, and efficient powder coating lines from Hangzhou Huaxiang Coating Equipment Co., Ltd. Designed for reliability and high-quality finishes, our solutions meet all your industrial powder coating machine needs. Contact us at sale3@cncolourspray.com