In the powder coating industry, the Electrostatic Powder Coating Oven is a revolutionary device that enables the achievement of high - quality cured finishes.
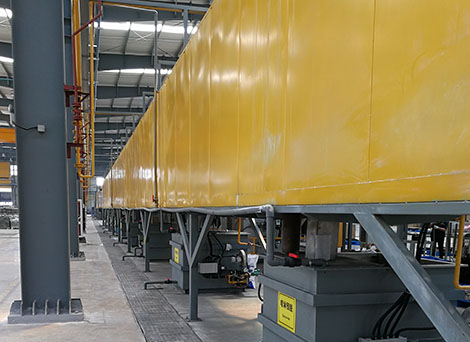
An
Electrostatic Powder Coating Oven is a specialized heating unit. Its chamber is constructed from robust, high - temperature - resistant materials such as stainless steel. The oven is equipped with electrostatic charging elements that are seamlessly integrated into the heating process. These elements play a crucial role in enhancing the adhesion of the powder coating during the curing stage. Inside the oven, heating elements, typically quartz or infrared heaters, are employed to generate heat. A circulation system, consisting of fans and ducts, ensures uniform heat distribution. Additionally, a precise temperature - control system with sensors is in place to maintain the ideal curing temperature.
Automotive manufacturers utilize these ovens to cure powder coatings on car bodies, resulting in a smooth and durable finish. Electronics companies rely on them to coat and cure the metal enclosures of devices, providing protection and a sleek appearance. Metal furniture producers use electrostatic powder coating ovens to harden the powder coatings on metal frames, enhancing both their appearance and durability.
Basic
Electrostatic Powder Coating Ovens for small - scale use typically start at around $5000 - $10000. They feature fundamental electrostatic capabilities and a straightforward heating setup. Mid - range ovens, equipped with improved electrostatic charging and more accurate temperature control, are priced between $10000 - $20000. High - end industrial - grade ovens, outfitted with advanced electrostatic technology and intelligent temperature - control systems, can cost upwards of $20000.
Prior to use, pre - heat the oven to the required curing temperature as per the powder's specifications. Ensure that the electrostatic charging system is functioning correctly. Place the powder - coated workpieces evenly within the oven. During the curing process, closely monitor the temperature and electrostatic charge. After curing, allow the oven to cool down before opening the door.
Take your production volume into consideration. High - volume production demands a high - end oven with rapid - heating capabilities and advanced electrostatic features. Evaluate the size of your workpieces; large items necessitate an oven with a spacious interior. Set a budget that aligns with your long - term production plans.
Wear heat - resistant gloves and safety goggles. Ensure proper ventilation in the area where the oven is located. Do not touch the oven's interior or workpieces immediately after the curing process, as they are extremely hot.
The electrostatic charging during the curing process significantly improves powder adhesion, leading to a more durable finish. The uniform heat distribution ensures a consistent cure, thereby enhancing the quality of the product. The precise temperature control minimizes the risk of over - curing or under - curing.
Q: What if the powder coating peels off after curing?
A: Check the electrostatic charging system and the surface preparation of the workpiece. Ensure that the powder adheres properly before curing.
Q: Can I use different powder types in the same oven?
A: Yes, but clean the oven thoroughly between powder type changes to prevent contamination.
Q: How often should I maintain the electrostatic charging system?
A: Inspect the electrostatic charging system monthly and clean it after every few uses to maintain optimal performance.
Q: What if the oven temperature fluctuates during curing?
A: Check the temperature - control system and sensors. They may require calibration or replacement.
Q: Can I upgrade the electrostatic charging system of the oven?
A: It may be possible. Consult the manufacturer regarding compatible upgrades and installation procedures