The following are the key operation points of the Electrostatic Powder Coating Machine
Surface pretreatment:
Thoroughly clean the surface of the object to be coated to remove impurities such as grease, dirt, and rust. Solvent cleaning, mechanical grinding, or chemical derusting methods can be used. For example, for oil stains on metal surfaces, a special metal cleaner can be used for wiping; for rust, it can be sanded until the metal luster is exposed or a rust remover can be used.
Appropriate roughening treatment of the surface (such as sanding) can enhance the adhesion of the powder, but pay attention to controlling the degree of grinding to avoid excessive damage to the object surface.
Equipment parameter adjustment:
Voltage and current settings: According to the type of powder and the characteristics of the object to be coated, reasonably adjust the voltage and current of the electrostatic generator. Generally, for thinner or more sensitive objects, the voltage and current should be appropriately reduced to prevent the uneven adsorption of powder or breakdown caused by an overly strong electrostatic field; for large-area, thick objects, the voltage and current can be appropriately increased to ensure sufficient powder adsorption. For example, when coating small precision metal parts, the voltage can be set at 40 - 60 kV and the current at 10 - 20 μA; when coating large metal plates, the voltage can be increased to 60 - 80 kV and the current to 20 - 30 μA.
Powder flow rate adjustment: According to the size and shape of the object, accurately control the powder flow rate. For small and complex objects, a smaller powder flow rate is required to achieve precise spraying; for large-area flat objects, the powder flow rate can be appropriately increased to improve spraying efficiency. It can be adjusted by the flow rate adjustment knob on the powder feeder or by inputting corresponding parameters in the equipment control system. For example, when spraying a small metal sculpture, the powder flow rate can be set at 50 - 100 g/min; when spraying a large metal cabinet, the powder flow rate can be increased to 200 - 300 g/min.
Air pressure adjustment: Adjust the air pressure of the spray gun to control the atomization effect and spraying range of the powder. Appropriate air pressure can evenly disperse the powder into fine particles and accurately spray it onto the object surface. Generally, an air pressure between 2 - 4 bar is more appropriate, but the specific value also needs to be fine-tuned according to the particle size of the powder and the model of the spray gun. For example, when using finer powder, the air pressure can be slightly lower, such as 2 - 3 bar; when using coarser powder, the air pressure can be increased to 3 - 4 bar.
Spray gun operation skills:
Spray gun distance control: Keep an appropriate distance between the spray gun and the surface of the object to be coated, usually between 15 - 30 cm. If the distance is too close, it may cause powder accumulation, resulting in sagging or orange peel phenomena; if the distance is too far, the powder will be unevenly dispersed, affecting the adhesion and appearance quality of the coating. During the spraying process, flexibly adjust the spray gun distance according to the shape and surface condition of the object. For example, when spraying the edges and corners of the object, the spray gun distance can be appropriately reduced to ensure sufficient powder coverage; when spraying a large flat surface, a relatively stable and moderate distance is maintained.
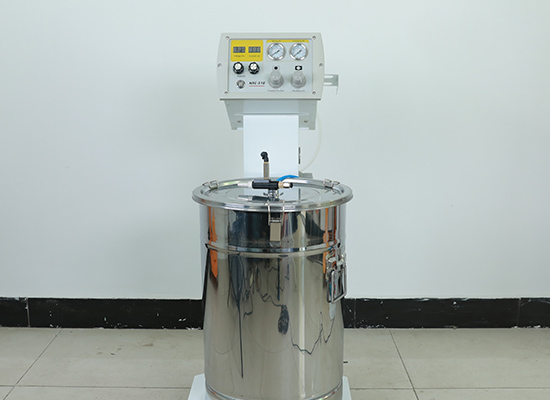
Spray gun moving speed: The spray gun should move at a constant speed, avoiding being too fast or too slow. If the moving speed is too fast, the thickness of the powder coating will be uneven; if it is too slow, excessive powder accumulation may occur. Generally, a spray gun moving speed of 30 - 60 cm/s is more appropriate. For example, when spraying a simple flat object, a faster moving speed can be used; when spraying an object with a complex shape and many details, the moving speed needs to be appropriately slowed down to ensure that the powder evenly covers all parts.
Spray angle adjustment: Try to keep the spray gun perpendicular to the object surface to ensure that the powder adheres evenly. When spraying objects with curved or inclined surfaces, continuously adjust the spray gun angle so that the powder can adhere smoothly to all parts of the object, avoiding undercoating or uneven coating thickness.
Curing process control:
Place the object coated with powder into the curing oven for curing treatment. The curing temperature and time should be strictly set according to the type of powder and the parameters recommended by the manufacturer. Generally, the common powder curing temperature is between 180 - 220°C, and the curing time is 10 - 30 minutes. For example, for some epoxy powder coatings, the curing temperature can be set at 180 - 200°C, and the curing time is 20 - 30 minutes; for polyester powder coatings, the curing temperature may be 200 - 220°C, and the curing time is 10 - 20 minutes.
During the curing process, ensure that the temperature in the curing oven is evenly distributed. Temperature sensors can be installed for monitoring and adjustment. At the same time, pay attention to avoiding collisions or other external forces on the object in the curing oven to prevent damage to the integrity of the coating.
Title:The following are the key operation points of the Electrostatic Powder Coating Machine
Link:http://www.hpowdercoating.com/pcms/show/433.html
Disclaimer: Enhance your coating process with advanced electrostatic powder coating machines, precision powder coating spray guns, comprehensive powder coating systems, and efficient powder coating lines from Hangzhou Huaxiang Coating Equipment Co., Ltd. Designed for reliability and high-quality finishes, our solutions meet all your industrial powder coating machine needs. Contact us at sale3@cncolourspray.com
Keywords:
Electrostatic Powder Coating Machine,Powder Coating Machine