Industrial Powder Coating Machine is a crucial asset in modern manufacturing processes, enabling the application of high - quality, durable powder coatings on a large scale.
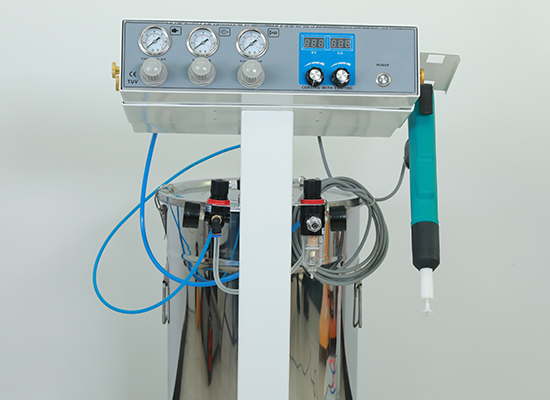
The working principle of an Industrial Powder Coating Machine is centered around electrostatic attraction. The machine typically uses a corona charging system. Here, a high - voltage electrode near the spray gun nozzle creates a corona discharge. As the powder passes through this ionized region, it acquires a negative charge. The object to be coated, which is grounded, then attracts these charged powder particles, resulting in an even coating. After application, the coated object is cured in an oven at a specific temperature for a set period. This curing process fuses the powder particles together, forming a hard, protective layer.
An Industrial Powder Coating Machine consists of several key components. The powder feeder is designed to store and dispense powder in a controlled manner. It can be of different types, such as a fluid - bed powder feeder or a vibratory powder feeder. The fluid - bed feeder, for example, uses air to fluidize the powder, ensuring a smooth and consistent flow. The spray gun is another vital part. It atomizes the powder into fine particles and directs them towards the object. The nozzles of the spray gun can be adjusted to create various spray patterns, like a wide - fan pattern for large - area coverage or a narrow - cone pattern for detailed work. The electrostatic generator provides the necessary high - voltage charge to the powder. The control panel allows operators to adjust parameters such as powder flow rate, air pressure, and electrostatic charge. The curing oven is designed to maintain a precise temperature range for proper powder curing.
The performance characteristics of an Industrial Powder Coating Machine are quite remarkable. It offers high transfer efficiency, meaning a significant portion of the sprayed powder adheres to the object. This reduces powder waste and cuts down on production costs. The machine can achieve a smooth and uniform finish, which is essential for industrial applications where aesthetics and quality are important. It can also handle a large volume of production, making it suitable for mass - manufacturing environments. Additionally, it can work with different types of powder, such as epoxy, polyester, and hybrid powders, each offering unique properties like corrosion resistance, heat resistance, and abrasion resistance.
Industrial Powder Coating Machines find applications in numerous industries. In the automotive industry, they are used to coat car bodies, wheels, and engine components. The durable coatings protect these parts from corrosion, wear, and environmental damage. In the construction industry, the machines are used to coat metal structures like steel beams, bridges, and building facades. This provides long - term protection against rust and weathering. In the electronics industry, they are used to coat electronic enclosures, offering protection against electromagnetic interference and physical damage.
When operating an Industrial Powder Coating Machine, proper surface preparation of the object is of utmost importance. The surface must be clean, free from grease, dirt, and rust. This can be achieved through methods like degreasing, sandblasting, or chemical cleaning. Operators need to adjust the machine settings according to the object's size, shape, and the type of powder being used. For example, for a large, flat metal sheet, a higher powder flow rate and a wide - fan spray pattern may be suitable. The distance between the spray gun and the object should be maintained at an appropriate range, usually around 15 - 30 cm.
Maintenance of an Industrial Powder Coating Machine is essential for its long - term performance. Regularly clean the powder feeder to prevent powder caking and ensure a smooth powder flow. The spray gun should be cleaned after each use to avoid clogging. Check the electrostatic generator for any malfunctions and ensure it is providing a stable charge. The curing oven needs to be calibrated regularly to maintain accurate temperature control. Replace any worn - out parts, such as nozzles and filters, in a timely manner.
Some common problems with Industrial Powder Coating Machines include uneven coating, which can be caused by incorrect spray gun settings, a malfunctioning electrostatic generator, or improper powder flow. Poor powder adhesion may be due to improper surface preparation or a problem with the powder's quality. To solve these issues, carefully check and adjust the relevant parameters, ensure proper surface treatment, and test the powder quality.
Disclaimer: Enhance your coating process with advanced electrostatic powder coating machines, precision powder coating spray guns, comprehensive powder coating systems, and efficient powder coating lines from Hangzhou Huaxiang Coating Equipment Co., Ltd. Designed for reliability and high-quality finishes, our solutions meet all your industrial powder coating machine needs. Contact us at sale3@cncolourspray.com