In the highly competitive powder coating industry, the Electrostatic Powder Coating Booth emerges as a revolutionary asset, redefining the standards for achieving high - quality and efficient powder coatings.
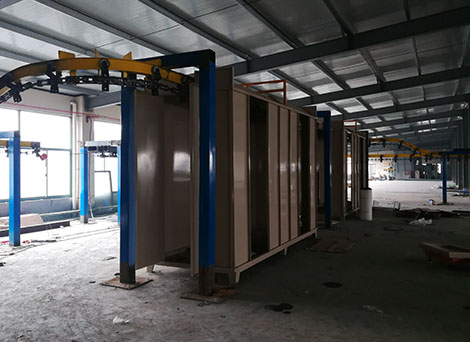
Introduction and Structure
An
Electrostatic Powder Coating Booth is a meticulously engineered and specialized enclosure. At its core lies a high - performance ventilation system, featuring industrial - grade exhaust fans paired with precisely designed ducts. This system is tasked with the crucial job of extracting over - sprayed powder, ensuring a clean and safe working environment.
Integrated within the booth is a state - of - the - art electrostatic charging system. As the powder is sprayed, this system imparts a uniform electric charge to it. This charged powder is then powerfully attracted to the grounded workpiece, resulting in significantly enhanced adhesion and a more durable and even coating.
Inside the booth, advanced powder - reclaim units such as high - efficiency cyclones or precision cartridge filters are installed. These components are responsible for collecting and recycling the excess powder, not only reducing material waste but also cutting down on production costs. To facilitate accurate spraying operations, the booth is equipped with bright, energy - efficient lighting fixtures that provide optimal illumination, allowing operators to achieve precision in every application.
Application Scenarios
In the automotive manufacturing sector, these booths are an essential part of the production line. They are used to coat car bodies and parts, guaranteeing a smooth, scratch - resistant, and long - lasting finish that meets the stringent quality standards of the automotive industry.
Metal furniture manufacturers heavily rely on electrostatic powder coating booths to coat large - scale metal frames. The electrostatic charging technology ensures that the powder adheres evenly, enhancing the appearance of the furniture while also providing excellent corrosion resistance, extending the lifespan of the products.
For the electronics industry, where aesthetics and protection are equally important, these booths are utilized to coat metal enclosures of devices. The result is a sleek, professional look combined with reliable protection against environmental factors.
Equipment Prices
For small - scale enterprises or those just starting in powder coating, basic electrostatic powder coating booths offer an affordable entry point. Priced in the range of (3000 - )8000, these booths come with fundamental electrostatic features and a straightforward ventilation setup. They are suitable for low - volume production and simple powder - coating tasks.
Mid - range booths, with their upgraded electrostatic components and enhanced powder - reclaim capabilities, are priced between (8000 - )15000. They offer better performance and durability, making them ideal for medium - sized operations that require more consistent powder coating and efficient powder recovery.
High - end industrial - grade booths, equipped with top - of - the - line electrostatic technology and high - efficiency ventilation systems, can cost upwards of $15000. These booths are engineered for large - scale production facilities, delivering maximum productivity, precision, and cost - effectiveness in the long run.
Correct Usage
Before commencing any powder - coating operations, it is imperative to conduct a thorough pre - start check. Ensure that the electrostatic charging system is calibrated correctly and the ventilation system is running smoothly. Securely ground the workpiece to ensure proper powder adhesion. Based on the type of powder and the material of the workpiece, carefully adjust the electrostatic voltage to achieve the optimal coating effect.
During the spraying process, maintain a consistent distance of about 15 - 20 cm between the gun and the workpiece. Move the gun at a steady speed to ensure an even application of the powder. After the spraying is complete, allow the ventilation system to run for a few more minutes to clear any remaining powder particles in the air. Then, clean the booth and the powder - reclaim system thoroughly to prevent powder buildup, which could affect the performance of the equipment over time.
Selection Tips
When choosing an
Electrostatic Powder Coating Booth, production volume is a key factor to consider. High - volume production facilities require high - end booths with advanced features such as automated powder - reclaim systems and precise electrostatic control. These booths can handle large - scale production demands without compromising on quality.
The types of workpieces also play a crucial role in the selection process. If you are dealing with complex - shaped workpieces, look for a booth with adjustable electrostatic settings. This will allow you to customize the coating process to ensure that every part of the workpiece receives an even coat.
Setting a budget that aligns with your long - term production plans is essential. While it may be tempting to opt for a cheaper option initially, investing in a higher - quality booth can save you money in the long run through reduced maintenance costs, improved productivity, and better - quality coatings.
Safety Precautions
Safety should always be a top priority when operating an electrostatic powder coating booth. Wear a high - quality dust mask to prevent the inhalation of powder particles, which can be harmful to your respiratory system. Protect your eyes with safety goggles to avoid any potential splashes or irritation. Gloves should be worn to safeguard your hands from powder contact and any possible chemical reactions.
Work in a well - ventilated area to minimize the risk of powder - related hazards. Powder particles in the air can be combustible, so proper ventilation helps to dissipate them and reduce the risk of fire or explosion. Additionally, ensure proper grounding of the electrostatic system to prevent electrical accidents. This includes regularly checking the grounding connections and using appropriate electrical safety devices.
Rationality Analysis
The electrostatic charging mechanism is a game - changer in the powder - coating process. By significantly improving powder adhesion, it reduces the amount of powder wasted during the coating process. This not only saves on material costs but also contributes to a more sustainable production process.
The powder - reclaim system further enhances the cost - effectiveness of the booth. By recycling excess powder, it cuts down on the need to purchase new powder frequently, resulting in substantial savings over time.
The overall design of the booth, with its focus on safety, efficiency, and precision, ensures a smooth and reliable powder - coating process. The well - designed ventilation system, advanced electrostatic charging system, and efficient powder - reclaim units work in harmony to create an optimal working environment.
Q&A
Q: What if the powder coating is uneven?
A: First, check the electrostatic voltage settings. An incorrect voltage can lead to inconsistent powder adhesion. Next, ensure that the distance between the gun and the workpiece is maintained consistently throughout the spraying process. If necessary, adjust the powder - flow rate to achieve a more even coating. Also, check the spray gun for any blockages or malfunctions that could affect the powder distribution.
Q: Can I use different powder types?
A: Yes, you can use different powder types in the same booth. However, it is crucial to clean the booth and the powder - reclaim system thoroughly between powder changes. Different powder types may have different particle sizes, chemical compositions, and electrostatic properties. Residual powder from a previous type can contaminate the new powder and affect the coating quality.
Q: How often should I clean the electrostatic charging system?
A: To maintain optimal performance, clean the electrostatic charging system every few uses. This helps to remove any powder residue that may have accumulated on the charging components. Use a soft brush or compressed air to gently clean the system, being careful not to damage any delicate parts. Regular cleaning ensures that the electrostatic charging system functions properly and provides consistent results.
Q: What if the powder doesn't adhere well?
A: Ensure that the workpiece is properly grounded. A poor ground connection can prevent the charged powder from adhering effectively. Check the electrostatic charge settings on the booth. If the charge is too low, the powder may not stick to the workpiece. Also, make sure the workpiece surface is clean and free of contaminants such as oil, grease, or dust, as these can interfere with powder adhesion.
Q: Can I upgrade the electrostatic charging system?
A: It may be possible to upgrade the electrostatic charging system, but it is essential to check with the manufacturer first. The manufacturer can provide guidance on the compatibility of different upgrades and ensure that the new system is suitable for your booth. Upgrading the electrostatic charging system can improve the coating quality and efficiency, but it should be done with caution to avoid any potential issues.
Disclaimer: Enhance your coating process with advanced electrostatic powder coating machines, precision powder coating spray guns, comprehensive powder coating systems, and efficient powder coating lines from Hangzhou Huaxiang Coating Equipment Co., Ltd. Designed for reliability and high-quality finishes, our solutions meet all your industrial powder coating machine needs. Contact us at sale3@cncolourspray.com