Electrostatic Powder Coat Spray Gun demand spans automotive, construction, and consumer goods sectors, driven by need for durable, eco-friendly finishes. Prices vary: entry-level handheld models start at $250, mid-range professional tools cost $800-$3,000, and industrial automated systems reach $10,000-$20,000, reflecting differences in precision, powder capacity, and automation features.
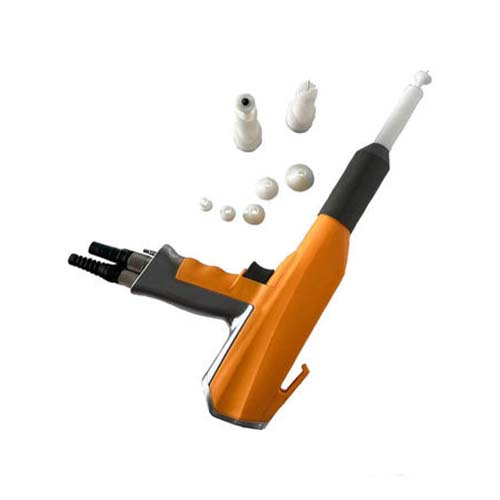
Electrostatic Powder Coat Spray Gun coating projects cover diverse applications, from coating steel doors and window frames to finishing bicycle frames and kitchen appliances. These projects prioritize a smooth, consistent layer that withstands harsh weather, chemicals, and daily wear. Whether for decorative purposes on metal furniture or protective coating on industrial pipes, the
Electrostatic Powder Coat Spray Gun delivers reliable results, making it a preferred choice for both small workshops and large manufacturing facilities.
Electrostatic Powder Coat Spray Gun surface treatment process technology starts with removing contaminants. This involves degreasing to eliminate oils, followed by abrasive blasting to remove rust or old coatings, creating a rough surface for better adhesion. Next, a conversion coating (like chromate or zirconium) is applied to prevent oxidation. The surface is then dried thoroughly to avoid moisture trapping. Proper treatment ensures the powder, applied via the Electrostatic Powder Coat Spray Gun, bonds firmly, reducing peeling and extending coating longevity.
Electrostatic Powder Coat Spray Gun is a device that applies dry powder coating to surfaces using electrostatic attraction. The gun imparts an electric charge to powder particles, which are drawn to the grounded workpiece. After application, the workpiece is heated in an oven, causing the powder to melt, flow, and cure into a hard, uniform film. Unlike liquid paint sprayers, it uses no solvents, making it a more sustainable option for creating protective and decorative layers.
Spray Nozzle: The tip of the Electrostatic Powder Coat Spray Gun that controls powder dispersion. It comes in various sizes—narrow nozzles for detailed areas, wide nozzles for large surfaces—ensuring precise coverage based on project needs.
Powder Hopper: A container attached to the Electrostatic Powder Coat Spray Gun that holds the coating powder. It often includes agitators to prevent clumping, maintaining a steady flow of powder to the nozzle during operation.
Control Unit: Houses the electrostatic generator and flow regulators. It adjusts voltage (typically 50-100kV) to control charge intensity and regulates powder output, allowing operators to fine-tune settings for different materials and surface types.
Electrostatic Powder Coat Spray Gun offers notable advantages. It reduces material waste as overspray can be collected and reused, lowering costs. The process contains no volatile organic compounds (VOCs), meeting strict environmental standards. Coatings applied with the Electrostatic Powder Coat Spray Gun are thicker and more resistant to impact than liquid paints, reducing the need for touch-ups. It also supports a wide range of colors and finishes, from matte to high-gloss, enhancing design flexibility.
Cleaning and maintaining an
Electrostatic Powder Coat Spray Gun properly ensures consistent performance. After each use, disconnect the gun from power and empty remaining powder from the hopper into its original container. Use compressed air to blow out the nozzle and powder lines, removing residual powder that could clog passages. Wipe the gun body with a soft brush to remove dust—avoid water, as moisture can damage the electrostatic generator. Weekly, inspect the nozzle for wear; replace it if edges are rounded to maintain proper spray pattern. Check the hopper’s agitator for debris and lubricate moving parts with manufacturer-recommended oil. Every month, test the electrostatic generator using a voltage meter to ensure it delivers consistent charge—fluctuations can cause uneven coating. Using a dedicated cleaning kit designed for your
Electrostatic Powder Coat Spray Gun model prevents damage, ensuring it remains reliable for long-term use.
Choosing an
Electrostatic Powder Coat Spray Gun for plastic surfaces requires specific considerations. Plastic conducts less electricity than metal, so select a gun with adjustable low-voltage settings (30-60kV) to avoid overcharging, which can cause powder buildup. Look for a lightweight design—plastic surfaces are often less rigid, and a heavy gun may lead to operator fatigue during extended use. Check powder flow control; plastic’s lower heat resistance (compared to metal) requires slower, more controlled powder application to prevent uneven curing. Ensure the gun is compatible with low-temperature curing powders, as high-heat powders can warp plastic. Testing the gun on a scrap plastic piece helps verify it delivers a smooth, adherent coating without damaging the substrate. Opting for a model with a narrow nozzle aids in coating intricate plastic parts with recessed areas.
Fixing bubbles in coatings applied with an Electrostatic Powder Coat Spray Gun involves identifying root causes. Bubbles often result from trapped air or moisture in the substrate. First, check surface preparation: ensure the plastic or metal was fully dried before coating—moisture evaporates during curing, forming bubbles. If the substrate is porous, pre-heat it gently (below curing temperature) to release trapped air before applying powder with the
Electrostatic Powder Coat Spray Gun. Adjust powder application: applying too thick a layer can trap air; reduce flow rate and make multiple thin passes instead. Check curing oven temperature—uneven heat (hot spots) can cause bubbles; use an oven thermometer to ensure consistent heat distribution. If bubbles persist, inspect the
Electrostatic Powder Coat Spray Gun’s nozzle for clogs, which disrupt powder flow and create uneven layers. Sanding the bubbled area, re-treating the surface, and reapplying powder with adjusted settings typically resolves the issue.
Adjusting settings on an
Electrostatic Powder Coat Spray Gun for different powder types ensures optimal results. For thermoplastic powders (melt and cool without chemical change), lower the electrostatic charge (40-60kV) to prevent clumping, as they are more sensitive to charge intensity. Increase powder flow rate slightly, as thermoplastics require a thicker layer for durability. For thermoset powders (chemically cure when heated), use higher voltage (70-100kV) to ensure deep adhesion, especially on textured surfaces. Reduce flow rate to avoid excess powder, which can cause uneven curing. For metallic powders, use a medium voltage (50-70kV) and a wide nozzle to distribute metal flakes evenly. Adjust the gun-to-substrate distance: closer (6-8 inches) for fine powders, farther (10-12 inches) for coarser varieties. Testing settings on a sample piece with each powder type helps dial in the perfect configuration for your Electrostatic Powder Coat Spray Gun.
Ensuring static safety when using an
Electrostatic Powder Coat Spray Gun is key to preventing accidents. Always ground both the workpiece and the gun using heavy-gauge copper cables connected to a dedicated ground rod—this dissipates excess static charge. Wear anti-static clothing and shoes to avoid personal static buildup, which can interfere with powder application or cause shocks. Keep the work area free of flammable materials (like solvents or rags), as airborne powder dust is combustible. Avoid operating the Electrostatic Powder Coat Spray Gun near water or damp surfaces, which can conduct electricity unpredictably. Never touch the nozzle or substrate while the gun is powered on. After use, discharge residual static by touching the grounded workpiece with a metal tool before handling the gun. Following these steps minimizes risks while maintaining efficient coating operations.
Disclaimer: Enhance your coating process with advanced electrostatic powder coating machines, precision powder coating spray guns, comprehensive powder coating systems, and efficient powder coating lines from Hangzhou Huaxiang Coating Equipment Co., Ltd. Designed for reliability and high-quality finishes, our solutions meet all your industrial powder coating machine needs. Contact us at gezx@cncolourspray.com