Electrostatic Powder Coating Gun System demand grows across automotive, aerospace, and construction sectors, driven by need for durable, cost-effective finishes. Prices vary: entry-level manual systems start at $1,500, mid-range semi-automatic setups cost $5,000-$15,000, and industrial fully automated systems reach $20,000-$100,000, based on capacity, precision, and automation features.
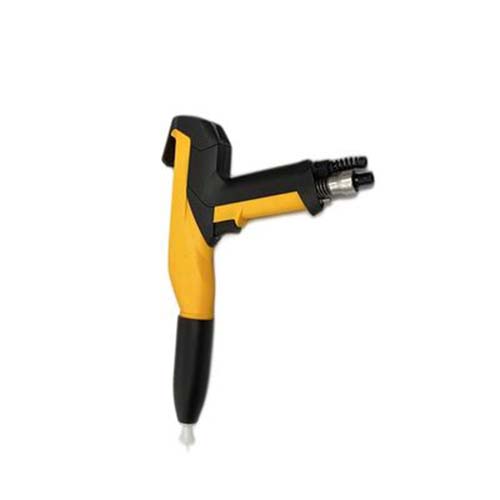
Electrostatic Powder Coating Gun System coating projects encompass a wide range, from coating automotive chassis and engine parts to finishing outdoor lighting fixtures and metal shelving. These projects focus on achieving a uniform, scratch-resistant layer that withstands corrosion and UV exposure. Whether for small-batch custom metalwork or high-volume appliance manufacturing, the
Electrostatic Powder Coating Gun System ensures consistent quality, making it integral to industries prioritizing both aesthetics and longevity.
Electrostatic Powder Coating Gun System surface treatment process technology begins with thorough cleaning. This involves alkaline degreasing to remove oils and greases, followed by acid etching to eliminate rust and scale. A rinse step removes chemical residues, then a conversion coating (such as iron phosphate) is applied to enhance powder adhesion. The surface is dried completely to prevent moisture from affecting the coating. Proper treatment ensures the powder, applied via the
Electrostatic Powder Coating Gun System, bonds tightly, reducing defects like pinholes or peeling.
Electrostatic Powder Coating Gun System is an integrated setup for applying dry powder coatings. It combines a spray gun, power supply, powder feeder, and often a curing oven. The gun charges powder particles, which adhere to grounded workpieces via electrostatic attraction. Post-application, the workpiece enters a curing oven where powder melts and cures into a hard, uniform film. This system replaces traditional liquid painting, offering a more efficient, eco-friendly method for protective and decorative coating.
Spray Gun Module: The handheld or robotic component of the
Electrostatic Powder Coating Gun System System that emits charged powder. It features adjustable nozzles and triggers, allowing operators to control spray pattern and intensity for different workpiece shapes.
Power Supply Unit: Regulates the electrostatic charge (typically 60-100kV) for the Electrostatic Powder Coating Gun System. It converts standard electrical current to high-voltage, low-amperage power, ensuring consistent particle charging for reliable adhesion.
Powder Delivery System: Includes a hopper, pumps, and hoses that transport powder from storage to the spray gun in the Electrostatic Powder Coating Gun System. It uses air pressure to maintain steady flow, with filters to prevent clogs and ensure powder purity.
Electrostatic Powder Coating Gun System offers key advantages. It reduces material waste by 95% compared to liquid paints, as overspray is recyclable. The process emits no volatile organic compounds (VOCs), aligning with global environmental regulations. Coatings applied via the Electrostatic Powder Coating Gun System are thicker (2-6 mils) and more impact-resistant than liquid layers, lowering long-term maintenance costs. It also supports fast color changes, enhancing production flexibility for custom orders.
Maintaining an
Electrostatic Powder Coating Gun System ensures consistent results and extends lifespan. Daily, disconnect power and clean the spray gun nozzle with compressed air to remove residual powder, preventing clogs. Wipe down hoses and hoppers to avoid powder buildup. Weekly, inspect the power supply unit for loose connections or damaged cords—tighten terminals and replace worn parts to maintain charge stability. Check powder delivery hoses for cracks; replace if damaged to prevent pressure loss. Monthly, calibrate the charge output using a voltage meter to ensure it matches manufacturer specs—imbalanced charge causes uneven coating. Lubricate moving parts in the feeder system with silicone-based oil to reduce friction. Using manufacturer-recommended cleaning agents and replacement parts specific to your Electrostatic Powder Coating Gun System model prevents malfunctions, keeping operations efficient.
Choosing the right
Electrostatic Powder Coating Gun System for high-volume production requires assessing key factors. First, evaluate throughput needs: systems with multiple robotic spray guns handle 500+ parts per hour, while single-gun setups suit lower volumes. Look for automated conveyor integration—synchronized with the curing oven, it reduces manual handling and speeds up cycles. Check powder capacity: hoppers holding 50+ pounds minimize refills, ideal for continuous runs. Prioritize systems with quick-change powder modules; swapping colors in under 10 minutes reduces downtime. Ensure the power supply offers adjustable voltage (80-100kV) to handle diverse part sizes, from small brackets to large panels. Testing the system with your specific powder type (thermoset or thermoplastic) confirms compatibility, ensuring the Electrostatic Powder Coating Gun System meets production targets without sacrificing quality.
Troubleshooting uneven coating with an
Electrostatic Powder Coating Gun System involves systematic checks. First, inspect the spray gun nozzle—wear or clogs disrupt spray pattern; replace or clean the nozzle to restore uniformity. Check powder flow rate: low flow causes thin spots, while high flow leads to buildup. Adjust the feeder pump pressure (typically 5-15 psi) to balance output. Verify workpiece grounding: poor grounding (loose cables or rusted clamps) causes uneven charge attraction. Clean ground connections and use conductive clamps to ensure consistent grounding. Check curing oven temperature—hot spots or cold zones cause uneven melting. Use oven sensors to map heat distribution and adjust settings. If issues persist, test the power supply’s charge output; fluctuations (common with worn components) disrupt particle adhesion. Calibrating or repairing the power unit often resolves uneven coating with the Electrostatic Powder Coating Gun System.
Adjusting parameters on an Electrostatic Powder Coating Gun System for different metal types ensures optimal adhesion. For aluminum, use lower voltage (50-70kV) to avoid arcing, as aluminum conducts electricity differently than steel. Reduce powder flow rate (10-20 grams per minute) to prevent thick layers that crack during curing. For steel, increase voltage (70-90kV) to ensure powder reaches recessed areas, with higher flow (20-30 grams per minute) for better coverage on rough surfaces. For galvanized steel, preheat the workpiece to 120-150°F before coating—this removes moisture and improves powder adherence. Adjust gun-to-workpiece distance: 8-10 inches for aluminum, 10-12 inches for steel, to balance coverage and avoid over-spray. Fine-tuning these parameters with your Electrostatic Powder Coating Gun System ensures consistent results across metal types.
Ensuring operator safety with an Electrostatic Powder Coating Gun System involves strict protocols. Operators must wear respirators approved for powder inhalation, safety glasses with side shields, and flame-resistant gloves. The workspace must have proper ventilation—local exhaust systems remove airborne powder, keeping concentrations below explosive limits. Ground all equipment (gun, conveyor, oven) with heavy-gauge cables connected to a dedicated earth ground to prevent static shocks. Post clear signs marking high-voltage zones; restrict access to trained personnel only. Never operate the Electrostatic Powder Coating Gun System with damaged cables or exposed wiring. After use, turn off power and discharge residual static by touching a grounded metal surface before cleaning. Regular safety training on system-specific hazards ensures operators understand risks, keeping the workplace secure.
Disclaimer: Enhance your coating process with advanced electrostatic powder coating machines, precision powder coating spray guns, comprehensive powder coating systems, and efficient powder coating lines from Hangzhou Huaxiang Coating Equipment Co., Ltd. Designed for reliability and high-quality finishes, our solutions meet all your industrial powder coating machine needs. Contact us at gezx@cncolourspray.com