The Industrial Powder Coating Oven market serves diverse sectors like automotive, aerospace, construction, and metal fabrication. Demand grows as industries seek durable, eco-friendly coating solutions. Prices vary: small batch ovens start around $5,000, mid-sized industrial models range from $15,000 to $50,000, and large custom systems exceed $100,000, depending on size, heating type (electric, gas), and automation level.
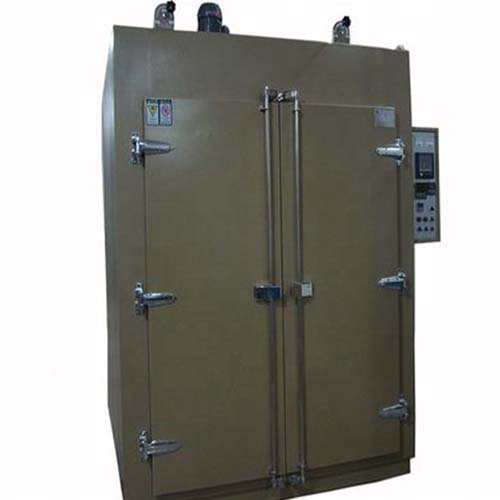
An
Industrial Powder Coating Oven is central to coating projects, integrating with powder spray booths and pre-treatment stations. Such projects typically involve preparing metal parts, applying dry powder, and curing in the oven. These projects aim to create a hard, uniform finish resistant to corrosion, impact, and weathering. Industries use them for items like car parts, machinery components, and architectural metalwork, ensuring long-lasting protection and aesthetic appeal.
Industrial Powder Coating Oven works with specific surface treatment technologies to ensure coating adhesion. The process starts with cleaning—removing oil, rust, and debris via chemical baths or sandblasting. Then, parts move to powder application, where electrostatic guns charge powder particles to adhere to the surface. The Industrial Powder Coating Oven then cures the powder at 350-450°F, melting and fusing it into a smooth, durable layer. This technology ensures better adhesion than liquid coatings, reducing chipping and peeling.
Industrial Powder Coating Oven is a specialized industrial equipment designed to cure powder coatings applied to metal and other substrates. It uses controlled heat to melt dry powder particles, forming a continuous, protective layer. Unlike liquid paint ovens, it operates without solvents, relying on thermal energy to bond the powder to the surface. These ovens come in various designs, including batch ovens for small-scale production and conveyor ovens for high-volume lines, adapting to different workpiece sizes and production needs.
Industrial Powder Coating Oven consists of three key components that work together for efficient curing.
Heating System: This provides the necessary heat using electric elements, gas burners, or infrared heaters. Electric systems suit smaller operations, while gas systems are common in large industrial setups for higher heat output.
Temperature Control System: Includes thermostats, sensors, and digital controllers to maintain precise temperatures (typically 350-450°F) crucial for proper curing.
Chamber and Ventilation: The insulated chamber retains heat, while ventilation systems remove fumes and excess moisture, ensuring consistent curing conditions and worker safety.
Industrial Powder Coating Oven offers multiple benefits over traditional liquid coating methods. It produces thicker, more uniform coatings with fewer drips or runs. The process is eco-friendly as it uses no volatile organic compounds (VOCs), reducing environmental impact and regulatory compliance costs. Coatings cured in these ovens are highly resistant to scratches, chemicals, and UV damage, extending workpiece lifespan. Additionally, powder overspray can be recycled, minimizing material waste and lowering production costs.
When selecting an
Industrial Powder Coating Oven size, first assess your largest workpiece dimensions, including height, width, and length. Ensure the oven chamber can accommodate these with extra space for air circulation—poor circulation leads to uneven curing. Next, consider production volume: high-volume lines need larger, conveyorized ovens to handle continuous throughput, while small batches may use compact batch ovens. Factor in future growth too; choosing a slightly larger oven avoids costly upgrades later. Match the size to your heating source capacity—an undersized oven for large parts will struggle to reach required temperatures, wasting energy and time.
Maintaining an Industrial Powder Coating Oven involves regular cleaning to remove powder residue from the chamber, heating elements, and vents—buildup insulates heat sources and causes temperature fluctuations. Inspect heating elements or burners monthly for damage; replace worn parts to prevent uneven heating. Check door seals for cracks, as leaks reduce efficiency and increase energy use. Calibrate temperature controls quarterly using a certified thermometer to ensure accuracy—incorrect temperatures ruin coatings. Lubricate conveyor systems (if applicable) to prevent jams, and clean ventilation filters weekly to maintain proper airflow. Document all maintenance to track issues and schedule proactive repairs, extending the oven’s lifespan.
Troubleshooting temperature inconsistencies in
Industrial Powder Coating Oven starts with checking the temperature sensor—dust or misalignment can cause incorrect readings; clean and reposition it. Inspect heating elements: burned-out or weak elements create cold spots, so test each for proper function and replace faulty ones. Check chamber insulation for gaps; heat loss in one area leads to uneven temperatures, so seal cracks with high-temperature sealant. Ventilation issues may also cause problems—excess airflow from open doors or broken dampers disrupts heat distribution, so ensure doors close tightly and adjust dampers to balance airflow. If using a conveyor oven, confirm consistent speed; slow or erratic movement leads to over-curing in some sections and under-curing in others.
Optimizing energy efficiency in
Industrial Powder Coating Oven operations begins with preheating only when needed—avoid leaving the oven on idle for long periods. Use programmable controls to set precise curing times and temperatures, preventing overheating. Insulate the chamber thoroughly, including doors and access panels, to reduce heat loss. Install a recirculation fan to distribute heat evenly, reducing the need for higher temperatures. Match the oven load to its capacity; running partially loaded ovens wastes energy, so batch similar-sized parts to fill the chamber. For gas ovens, ensure burners are properly adjusted for complete combustion—inefficient burning increases fuel use. Consider upgrading to an energy-efficient model with variable speed fans and high-efficiency heating elements for long-term savings.
Ensuring safety when operating
Industrial Powder Coating Oven requires training workers on proper procedures, including never opening the oven during curing—high temperatures can cause burns or release harmful fumes. Equip the workspace with fire extinguishers rated for powder and electrical/gas fires, as excess powder is combustible. Install gas detectors (for gas-powered ovens) to alert of leaks, and ensure proper ventilation to remove fumes, preventing respiratory issues. Never block vents or overload the chamber, as this disrupts airflow and increases fire risk. Use heat-resistant gloves and protective clothing when handling hot parts, and post clear warning signs around the oven area. Regularly inspect emergency shut-off switches to ensure they function, allowing quick shutdowns in case of emergencies.
Disclaimer: Enhance your coating process with advanced electrostatic powder coating machines, precision powder coating spray guns, comprehensive powder coating systems, and efficient powder coating lines from Hangzhou Huaxiang Coating Equipment Co., Ltd. Designed for reliability and high-quality finishes, our solutions meet all your industrial powder coating machine needs. Contact us at gezx@cncolourspray.com