The market for Powder Coating Oven Manufacturer services grows as industries like automotive, aerospace, and construction demand durable coating solutions. Manufacturers cater to small workshops and large factories, with prices varying by customization: standard ovens from $10,000-$50,000, custom large-scale systems exceeding $100,000, based on size, heating type, and tech.
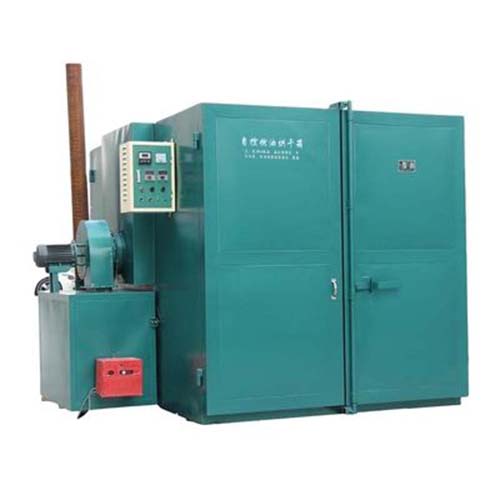
Powder Coating Oven Manufacturer plays a key role in coating projects by providing tailored equipment. These projects range from small-batch metal parts to large structural components. Manufacturers collaborate with clients to understand project needs—like curing temperature, throughput, and space constraints—then deliver ovens that integrate seamlessly. They often assist in project planning, ensuring the oven aligns with pre-treatment stations and spray booths for a smooth workflow, reducing delays and improving efficiency.
Powder Coating Oven Manufacturer drives advancements in surface treatment process technology. They develop ovens with precise temperature control (350-450°F) to match powder chemistry, ensuring proper adhesion. Many integrate infrared heating for faster curing or convection systems for uniform heat distribution. Manufacturers also test and refine ventilation designs, removing fumes without disrupting temperature stability, which is critical for consistent coating quality across all treated surfaces.
Powder Coating Oven Manufacturer is an entity that designs, engineers, and produces industrial ovens used to cure powder coatings. These manufacturers serve diverse sectors, from automotive repair shops to heavy machinery plants. They create various oven types: batch ovens for small volumes, conveyor ovens for mass production, and custom models for unique part sizes. Their work combines material science (heat-resistant metals, insulation) and engineering (heating systems, controls) to deliver functional, safe equipment.
Powder Coating Oven Manufacturer operates through three core components to deliver quality equipment.
R&D Department: Teams here design ovens, testing new heating technologies, insulation materials, and control systems. They adapt to industry trends, like energy efficiency, ensuring ovens meet evolving client needs.
Production Facility: Where raw materials (steel, heating elements) are assembled into ovens. Skilled workers use precision tools to build chambers, install controls, and test functionality, adhering to safety standards.
Client Support Team: Assists with installation, training, and maintenance. They help clients optimize oven use, troubleshoot issues, and provide replacement parts, ensuring long-term client satisfaction.
Powder Coating Oven Manufacturer offers distinct advantages for buyers. Reputable manufacturers produce ovens with durable materials, reducing breakdowns and extending lifespan. They provide custom solutions—adjusting size, heating type, or controls to fit unique workflows. Many include warranty packages, covering parts and labor, lowering long-term costs. Manufacturers with strong R&D ensure ovens are energy-efficient, cutting utility bills. Their expertise in compliance (safety, environmental regulations) helps clients avoid fines, making them valuable partners.
Evaluating a
Powder Coating Oven Manufacturer’s reliability starts with checking client reviews—look for consistent praise for on-time delivery and equipment performance. Request references and contact past clients to ask about post-purchase support, like response time to repair requests. Inspect the manufacturer’s certification: adherence to ISO standards or industry-specific certifications (like automotive QS 9000) indicates quality commitment. Review their warranty terms—a longer warranty (3+ years) shows confidence in their ovens. Assess their production capacity: can they handle your order size within your timeline? A reliable manufacturer will be transparent about capabilities and limitations, avoiding overpromising.
Comparing prices among
Powder Coating Oven Manufacturers requires looking beyond upfront costs. Request detailed quotes that break down components: chamber size, heating type, and controls. A lower price might mean thinner insulation or basic controls, increasing long-term energy or upgrade costs. Compare warranty inclusions—some manufacturers charge extra for service, while others include it. Factor in shipping and installation fees, which vary by location and manufacturer. Consider total cost of ownership: a slightly pricier oven with better efficiency may save more over 5 years than a cheaper, less efficient model. Ask about bulk discounts if ordering multiple units, as some manufacturers offer reduced rates for large orders.
Requesting custom designs from a Powder Coating Oven Manufacturer starts with detailing your needs: specify maximum part dimensions, required curing temperature range, and production volume. Include space constraints, like workshop width or ceiling height, to ensure the oven fits. Share your heating preference (electric, gas, infrared) and any special features, such as programmable controls or explosion-proof designs for hazardous environments. Provide drawings of parts to be coated, so the manufacturer can optimize chamber layout for airflow. Ask for a prototype or design mockup to review before production, ensuring it meets expectations. Discuss timeline and budget upfront to avoid delays or cost overruns, and get the custom specs in writing to confirm agreement.
Verifying a Powder Coating Oven Manufacturer’s compliance with safety standards involves checking for certifications from recognized bodies, like OSHA (U.S.) or CE (EU), which indicate adherence to electrical, fire, and ventilation safety rules. Request test reports from third-party labs showing the oven meets temperature stability and emissions limits. Inspect the manufacturer’s production facility (if possible) to see if safety protocols are followed during assembly, like proper wiring and insulation. Ask about safety features included: emergency shut-off switches, overheat protection, or door interlocks that prevent operation when open. A compliant manufacturer will readily provide documentation and explain how their ovens meet or exceed regional safety regulations.
Assessing after-sales service of a Powder Coating Oven Manufacturer starts with asking about service response time—do they offer 24/7 support or have local technicians? Inquire about spare parts availability: can they deliver critical parts (like heating elements) within 48 hours to minimize downtime? Review their maintenance packages: do they offer scheduled inspections or training for your team to perform basic upkeep? Check online forums for client complaints about unresponsive service, as consistent issues indicate poor support. A strong after-sales service includes a dedicated account manager who knows your oven model and history, ensuring personalized assistance when problems arise.
Determining if a Powder Coating Oven Manufacturer fits small business needs involves checking their range of small-scale ovens—do they offer compact models under 50 sq ft that fit in limited spaces? Ask about flexible payment terms, like financing or installment plans, to ease upfront costs. Assess their minimum order quantity: some manufacturers focus on large orders, but those catering to small businesses will accept single-unit orders. Inquire about training resources—do they provide user manuals, video tutorials, or on-site training for small teams with limited expertise? A good fit will prioritize small clients, offering the same attention to detail as large accounts, and adjust their support to match your business size.</think># Powder Coating Oven Manufacturer Guide to Quality and Selection
The market for Powder Coating Oven Manufacturer services grows as industries like automotive, aerospace, and construction demand durable coating solutions. Manufacturers cater to small workshops and large factories, with prices varying by customization: standard ovens from $10,000-$50,000, custom large-scale systems exceeding $100,000, based on size, heating type, and tech.
Powder Coating Oven Manufacturer supports coating projects by delivering equipment tailored to project scopes. Whether for coating automotive parts, architectural metal, or industrial machinery, manufacturers work with clients to design ovens that match production speed, part sizes, and curing requirements. They often collaborate from project initiation, advising on oven placement, integration with spray booths, and workflow optimization to ensure the coating process runs smoothly from pre-treatment to final curing.
Powder Coating Oven Manufacturer drives innovation in surface treatment process technology. They develop ovens with advanced heating systems—such as dual-mode (convection + infrared) heating—to reduce curing time while ensuring uniform coating. Manufacturers optimize temperature control algorithms, allowing precise adjustments for different powder types (epoxy, polyester). They also enhance ventilation systems to remove volatile byproducts, ensuring the surface treatment process meets environmental standards and produces consistent, high-adhesion finishes.
Powder Coating Oven Manufacturer is an entity that designs, produces, and distributes industrial ovens specifically for curing powder coatings. These manufacturers combine engineering expertise with material science to create ovens suitable for diverse substrates, including metal, plastic, and composite materials. They serve sectors ranging from small-scale fabrication shops to large manufacturing plants, offering both standard models and custom-built ovens tailored to unique operational needs.
Powder Coating Oven Manufacturer operates through three core components to deliver reliable equipment.
Engineering Team: Responsible for designing ovens, using CAD software to model chamber dimensions, heating element placement, and airflow patterns. They test designs via simulations to ensure thermal efficiency and safety before production.
Manufacturing Plant: Equipped with metalworking machinery to cut, weld, and assemble oven frames. Workers install heating elements, control panels, and insulation, following strict quality checks at each production stage.
Customer Service Division: Provides pre-sales consultations to understand client needs, assists with installation, and offers ongoing maintenance support. They troubleshoot issues, supply replacement parts, and train clients on optimal oven operation.
Powder Coating Oven Manufacturer offers key advantages for buyers. They deliver ovens built with high-grade materials—like stainless steel chambers and heat-resistant insulation—ensuring durability and long service life. Reputable manufacturers provide customization options, such as adjustable conveyor speeds or multi-zone temperature control, to align with specific production goals. They often include technical support, helping clients resolve operational issues quickly. Additionally, manufacturers staying updated on industry regulations ensure their ovens meet safety and environmental standards, reducing compliance risks for buyers.
Evaluating a Powder Coating Oven Manufacturer’s reliability involves checking their track record: review their years in business and portfolio of completed projects to gauge experience. Request case studies from clients in your industry to learn how their ovens performed in similar applications. Inspect their quality control processes—do they conduct rigorous testing (like thermal mapping) on each oven before shipment? Ask about their failure rate; a low rate (under 5% annually) indicates consistent quality. A reliable manufacturer will also be transparent about lead times and communicate proactively if delays occur.
Comparing prices among Powder Coating Oven Manufacturers requires analyzing the value behind the cost. Request itemized quotes that detail components: chamber material thickness, type of heating elements, and control system sophistication. A lower price may reflect basic features (manual controls, thin insulation) that increase energy use over time. Compare warranty coverage—some manufacturers offer longer terms for critical parts (heating elements, controllers) at a slightly higher price, which can reduce repair costs. Factor in delivery and installation fees, as these vary by manufacturer location and oven size. Consider long-term savings from energy-efficient models, which may offset higher upfront prices.
Requesting custom designs from a Powder Coating Oven Manufacturer starts with documenting your requirements: note maximum part dimensions, daily production volume, and required curing temperature range (typically 300-450°F). Specify space constraints, such as workshop width or ceiling height, to ensure the oven fits. Share details about your powder type, as some require specific airflow rates. Ask the manufacturer to provide a 3D design rendering for review, and request a prototype test with a sample part to verify curing quality. Discuss timeline milestones, including design approval, production start, and delivery, to keep the project on track.
Verifying a Powder Coating Oven Manufacturer’s compliance with safety standards involves checking for certifications like ISO 9001 (quality management) and OSHA compliance for electrical and fire safety. Request copies of test reports from accredited labs, confirming the oven meets temperature accuracy limits and emission thresholds. Inquire about safety features: does the oven include overheat alarms, emergency stop buttons, or flame-resistant insulation? Ask if their manufacturing process follows safety protocols, such as proper wiring for electrical ovens or gas leak detection systems for gas-powered models. A compliant manufacturer will readily share this documentation and explain how their ovens adhere to regional regulations.
Assessing after-sales service of a Powder Coating Oven Manufacturer includes asking about response times for service requests—ideally, they should offer 24-48 hour support for critical issues. Inquire about the availability of replacement parts; a manufacturer with a well-stocked parts warehouse can minimize downtime. Check if they provide maintenance contracts, offering 定期 inspections to prevent breakdowns. Read client reviews to learn about experiences with service quality—look for comments on technician expertise and resolution efficiency. A strong after-sales team will also provide training materials, like user manuals or video guides, to help clients operate the oven safely and efficiently.
Determining if a Powder Coating Oven Manufacturer fits small business needs involves checking if they offer compact oven models (under 100 cubic feet) suitable for limited workshop space. Ask about flexible payment options, such as leasing or installment plans, to ease upfront financial strain. Inquire about minimum order quantities—small businesses often need single units, so avoid manufacturers requiring large bulk orders. Assess their customer service for small accounts: do they provide the same level of support as for large clients? A good fit will offer personalized consultations to recommend cost-effective models and provide training tailored to small teams with limited technical expertise.
Disclaimer: Enhance your coating process with advanced electrostatic powder coating machines, precision powder coating spray guns, comprehensive powder coating systems, and efficient powder coating lines from Hangzhou Huaxiang Coating Equipment Co., Ltd. Designed for reliability and high-quality finishes, our solutions meet all your industrial powder coating machine needs. Contact us at gezx@cncolourspray.com