The Small Powder Coating Oven market sees high demand from small workshops, hobbyists, and small-scale manufacturers. These ovens suit projects like metal furniture, automotive parts, and custom crafts. Prices range: entry-level models start at $2,000-$4,000, mid-range at $4,000-$8,000, with features like better insulation and controls; premium compact units hit $8,000-$15,000 for advanced tech.
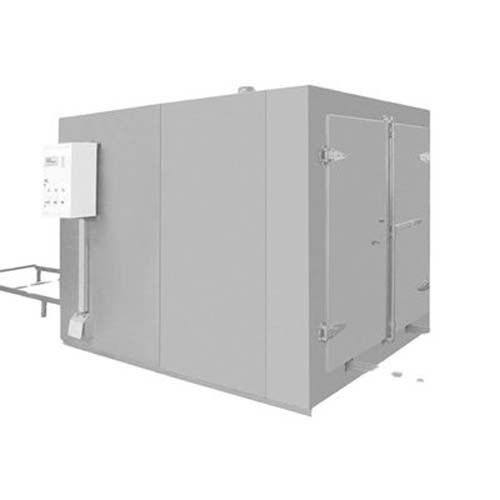
Small Powder Coating Oven plays a central role in small-scale coating projects. These projects often involve coating smaller metal items such as tools, bike frames, or decorative metal pieces. The process starts with cleaning the item to remove dirt and rust, then applying a powder coating using a spray gun. The item is then placed in the
Small Powder Coating Oven to cure, where heat melts the powder into a smooth, durable finish. Such projects focus on quality and precision, making the oven a key tool for achieving consistent results.
Small Powder Coating Oven works with specific surface treatment technology to ensure strong adhesion. First, the surface is pre-treated—this may involve sandblasting to create a rough texture or chemical cleaning to remove oils. Next, the powder is applied electrostatically, making particles stick to the surface. The
Small Powder Coating Oven then cures the powder at 320-420°F (160-215°C). This temperature range is critical: too low and the powder won’t melt properly; too high and it may discolor. The technology ensures the coating bonds tightly, resulting in a finish that resists chipping and corrosion.
Small Powder Coating Oven is a compact industrial device designed to cure powder coatings on small to medium-sized items. It uses controlled heat to turn dry powder into a hard, protective layer. Unlike larger industrial ovens, it has a smaller chamber, making it ideal for limited spaces. It operates without solvents, relying on electric or gas heating to reach the required curing temperatures. These ovens often come with basic or advanced temperature controls, allowing users to adjust settings based on the powder type and item size.
Heating Element: Most use electric heating coils or small gas burners. Electric elements are common in home workshops for their ease of use; gas burners suit those needing higher heat output with lower running costs.
Temperature Controller: A digital or analog device that monitors and adjusts the oven’s internal temperature. It ensures the temperature stays within the required range for consistent curing, with some models offering programmable settings.
Insulated Chamber: The inner space where items are placed. It is lined with heat-resistant insulation to retain heat, reduce energy loss, and keep external surfaces cool for safety.
Small Powder Coating Oven offers several advantages for small-scale operations. Its compact size fits in garages or small workshops, saving space. It uses less energy than larger ovens, cutting down on utility costs. The curing process produces minimal waste, as unused powder can be collected and reused. Coatings cured in a
Small Powder Coating Oven are durable, withstanding daily wear and tear better than paint. They also come in a wide range of colors and finishes, giving users creative flexibility. Additionally, these ovens are easy to operate, making them accessible to hobbyists with little experience.
Installing a
Small Powder Coating Oven in a home workshop requires choosing a well-ventilated area to disperse any fumes. Keep it away from flammable materials like paint thinners or wood dust—maintain at least 3 feet of clear space around it. For electric models, ensure the workshop has a dedicated circuit to handle the oven’s power needs; overloading circuits causes fires. For gas models, check gas lines for leaks using a soapy water test, and connect to a properly vented exhaust to remove combustion byproducts. Secure the oven on a level surface to prevent tipping, and install a fire extinguisher nearby. Read the manufacturer’s guidelines to follow specific installation steps for your model.
Adjusting temperature settings on a
Small Powder Coating Oven starts with checking the powder manufacturer’s instructions—each powder type (epoxy, polyester, or hybrid) has a specific curing temperature range. For example, epoxy powders often cure at 320-350°F, while polyester may need 350-400°F. Use the oven’s temperature controller to set the target temperature. Let the oven preheat fully, then test with a small sample piece—cure it, then check the finish. If it’s too soft, increase the temperature slightly; if it’s discolored, lower it. Keep a log of settings for different powders to replicate results easily, ensuring each coating cures perfectly.
Cleaning a
Small Powder Coating Oven regularly prevents powder residue buildup, which can contaminate new coatings. Wait for the oven to cool completely, then wipe the interior with a dry cloth to remove loose powder. For stubborn residue, use a soft brush or vacuum with a brush attachment—avoid harsh chemicals that may damage the chamber. Clean the heating elements gently to remove dust, which can block heat. Wipe the door seal to ensure it closes tightly, as a dirty seal allows heat loss. Finish by leaving the door open for a few hours to air out, keeping the interior dry and ready for the next use.
To determine if a
Small Powder Coating Oven suits your coating materials, first check the material’s curing requirements. Most powder coatings need temperatures between 300-450°F—ensure the oven can reach and maintain this range. Consider the material’s thickness: thicker coatings may need longer curing times, so check if the oven can run for extended periods without overheating. For heat-sensitive materials, see if the oven offers precise temperature control to avoid over-curing. Also, check the chamber size—ensure it fits your largest coated item with space for air flow, as poor flow affects material adhesion.
Troubleshooting uneven curing in a Small Powder Coating Oven starts with checking air circulation. Blocked vents or overcrowded chambers restrict airflow—leave space between items and clean vents. Next, test the temperature sensor: use an external thermometer to compare readings. If off, calibrate the sensor or replace it. Check the heating element—if part of it is damaged, it may heat one area more. Rotate items during curing to ensure all sides get equal heat. Also, verify the curing time: too short and some areas won’t cure; extend it slightly and test with a sample to find the right duration.
Disclaimer: Enhance your coating process with advanced electrostatic powder coating machines, precision powder coating spray guns, comprehensive powder coating systems, and efficient powder coating lines from Hangzhou Huaxiang Coating Equipment Co., Ltd. Designed for reliability and high-quality finishes, our solutions meet all your industrial powder coating machine needs. Contact us at gezx@cncolourspray.com