Aluminium Profile Powder Coating Line serves rising demands in construction automotive and furniture industries. It coats aluminium profiles used for windows doors curtain walls and vehicle frames. Prices range from $20000 for small batch lines to over $300000 for large automatic systems based on processing speed and automation level.
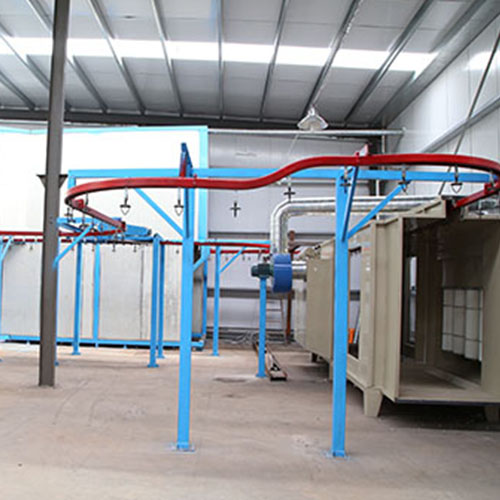
Aluminium Profile Powder Coating Line handles projects covering various aluminium profile sizes and shapes. These projects aim to apply uniform durable coatings that resist weather corrosion and UV damage. They cater to commercial construction projects residential building developments and industrial component manufacturing ensuring aluminium profiles meet both aesthetic and performance standards.
Aluminium Profile Powder Coating Line uses specific surface treatment steps to prepare profiles for coating. This includes alkaline degreasing to remove oils and dirt acid etching to smooth surfaces and conversion coating (chromate or non-chromate) to enhance powder adhesion. Process parameters like temperature (50-60°C for degreasing) and immersion time (3-5 minutes) are controlled to ensure consistent surface quality critical for coating durability.
Aluminium Profile Powder Coating Line is a specialized system designed to apply dry powder coatings to aluminium profiles through electrostatic deposition followed by heat curing. It integrates material handling surface preparation powder application and curing into a continuous process. This line transforms raw aluminium profiles into finished products with protective and decorative coatings suitable for diverse industrial and commercial uses.
Conveyor System: Transports aluminium profiles through each processing stage. It uses hanging hooks or racks to hold profiles securely adjusting speed (1-5 m/min) based on coating requirements to ensure uniform processing.
Pretreatment Tanks: A series of tanks for degreasing rinsing and conversion coating. These tanks use controlled chemical solutions to clean and condition aluminium surfaces preparing them for effective powder adhesion.
Powder Application Booth: Contains electrostatic spray guns that charge powder particles which adhere to grounded aluminium profiles. The booth includes a powder recovery system to collect and reuse excess powder reducing material waste.
Curing Oven: Heats coated profiles to 180-200°C for 10-20 minutes melting and fusing powder into a smooth hard film. Ovens feature precise temperature control to ensure proper curing without damaging aluminium profiles.
Aluminium Profile Powder Coating Line delivers uniform coating thickness across complex profile shapes reducing rework needs. It produces coatings with high impact resistance and color retention suitable for outdoor use. The process generates minimal volatile organic compounds making it environmentally friendly. It supports quick color changes allowing flexibility in production. Lower material waste and longer coating lifespan also reduce overall operational costs compared to liquid painting methods.
How to choose the right Aluminium Profile Powder Coating Line for different profile sizesTo choose the right
Aluminium Profile Powder Coating Line consider maximum profile length and width. Lines with adjustable conveyor hooks work for profiles 2-6 meters long. Check pretreatment tank dimensions to ensure full immersion of large profiles. For small intricate profiles select lines with fine-tipped spray guns for precise coating. Match curing oven length to profile size to ensure even heating; longer ovens suit longer profiles. Evaluate automation level—semi-automatic lines fit mixed size batches while fully automatic lines excel at consistent large profile production.
How to operate Aluminium Profile Powder Coating Line for optimal coating qualityOperate
Aluminium Profile Powder Coating Line by first calibrating spray gun voltage (60-80 kV) to ensure proper powder adhesion. Set conveyor speed to match profile size—slower speeds work for thick profiles needing more coating. Maintain powder flow rate (50-100 g/min) consistent across all guns. Monitor pretreatment chemical concentrations daily; adjust pH levels (6.5-7.5 for rinsing tanks) to prevent surface defects. In curing ovens verify temperature uniformity within ±5°C; uneven heat causes coating discoloration. Regularly clean spray booth filters to avoid powder contamination affecting finish quality.
How to maintain Aluminium Profile Powder Coating Line to prevent breakdownsMaintain
Aluminium Profile Powder Coating Line by cleaning spray guns daily to remove dried powder buildup that clogs nozzles. Lubricate conveyor chain every 50 hours of operation to prevent jamming. Inspect pretreatment pumps weekly for leaks and replace worn seals promptly. Check curing oven heating elements monthly; replace any that fail to reach set temperatures. Clean powder recovery filters monthly to maintain airflow and recovery efficiency. Keep a maintenance log to track part replacements and schedule preventive checks reducing unexpected breakdowns.
How to troubleshoot coating peeling issues in Aluminium Profile Powder Coating LineTroubleshoot coating peeling in
Aluminium Profile Powder Coating Line by first checking pretreatment steps. Inadequate degreasing leaves oils causing poor adhesion—test surface cleanliness with water break test (water should sheet evenly). If pretreatment is correct inspect curing parameters; insufficient time or temperature prevents full powder fusion—verify oven temperature with a portable thermometer. Check profile grounding; poor grounding reduces powder adhesion—ensure conveyor hooks make solid contact with profiles. Excessive powder thickness (over 120 microns) can also cause peeling; adjust spray gun settings to reduce application rate.
How to ensure workplace safety when using Aluminium Profile Powder Coating LineEnsure safety with
Aluminium Profile Powder Coating Line by equipping operators with chemical-resistant gloves and goggles for pretreatment tasks. Install ventilation systems in spray booths to keep powder dust below safe exposure limits. Mark emergency stop buttons along the line and train staff to use them. Inspect electrical connections in curing ovens regularly to prevent sparks near powder dust. Store powder in sealed containers away from heat sources. Follow lockout procedures during maintenance to prevent accidental line startup. Conduct monthly safety drills to reinforce proper handling of chemicals and equipment.
Disclaimer: Enhance your coating process with advanced electrostatic powder coating machines, precision powder coating spray guns, comprehensive powder coating systems, and efficient powder coating lines from Hangzhou Huaxiang Coating Equipment Co., Ltd. Designed for reliability and high-quality finishes, our solutions meet all your industrial powder coating machine needs. Contact us at gezx@cncolourspray.com